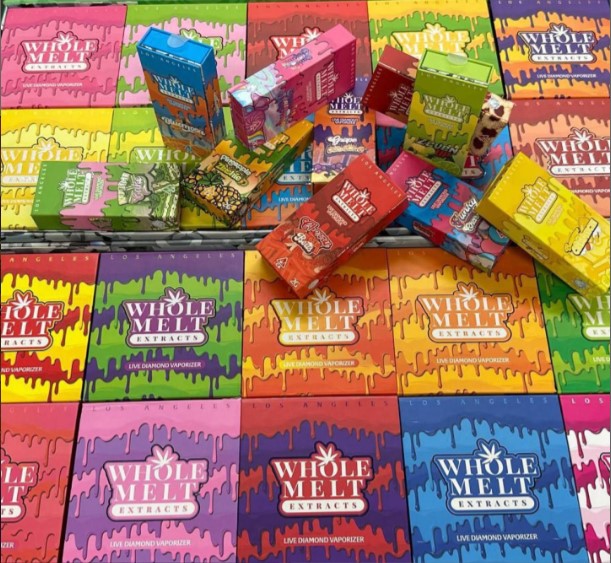
When aiming for the most standard of safety for your whole melt materials, our bulk packaging solutions are the perfect choice. We deliver a extensive range of options to meet your individual demands. From sturdy containers to specialized liners, we confirm that your whole melt is preserved throughout the entire distribution chain. Our experienced team is committed to helping you select the most packaging method for your business.
Efficient Whole Melt Bulk Material Handling
In the demanding realm of industrial processing, seamlessly managing bulk material flow is paramount. Whole melt bulk material handling presents a unique set of challenges, requiring systems that can accommodate large volumes of molten material with precision and minimal downtime. Advanced technologies are employed to ensure uniform melting, transfer, and distribution, meeting the click here stringent requirements of diverse industries. From processing facilities, seamless whole melt bulk material handling plays a crucial role in maximizing productivity and minimizing downtime.
Unlocking Efficiency with Whole Melt Bulk Processing
In the realm of metal fabrication, efficiency is paramount. Batch melt processing emerges as a leading technique to enhance production outputs. By melting and processing massive quantities of metal in a consolidated operation, this method considerably reduces production time. Furthermore, it minimizes the need for multiple melt cycles, thereby enhancing resource utilization and reducing overall costs.
- Whole melt bulk processing offers a streamlined approach to metal fabrication, enabling manufacturers to achieve greater efficiency and cost savings.
- The technique's ability to process large quantities of metal in a single operation significantly reduces processing time and resource consumption.
- By minimizing the number of melt cycles required, whole melt bulk processing contributes to a more sustainable and environmentally friendly manufacturing process.
The Future of Materials: Whole Melt Bulk Technology
Whole melt bulk technology is poised to transform the materials industry. This groundbreaking process involves heating raw materials in their entirety, allowing for the creation of complex structures with unprecedented accuracy. By eliminating the need for multiple fabrication steps,whole melt bulk technology offers significant improvements in terms of cost effectiveness, production volume, and material traits.
Applications for whole melt bulk technology are diverse, spanning industries such as aerospace, automotive, electronics, and medical devices. From high-strength alloys to flexible composites, the potential of this technology is limitless. As research and development continue to advance, we can expect to see even more revolutionary applications emerge in the years to come.
Maximizing Production with Whole Melt Bulk Systems
Implementing whole melt bulk systems can drastically transform your production processes. These innovative systems offer numerous advantages, leading to increased productivity and reduced expenses. By melting raw materials in large batches, manufacturers can streamline their operations, minimize downtime, and achieve greater control over the consistency of their final products.
- Additionally, whole melt bulk systems often incorporate advanced automation technologies, minimizing manual labor requirements and encouraging a safer working environment.
- As a result, businesses that adopt these systems can observe significant improvements in their overall production capacity and profitability.
The Journey from Prototyping to Production
Whole Melt Bulk delivers a robust solution for manufacturers seeking to efficiently bridge the gap between mold and market. By harnessing the strengths of bulk material processing, Whole Melt Bulk supports quicker production cycles, reduced lead times, and enhanced cost efficiency. This shift in manufacturing approaches allows companies to react quickly to shifting market demands, consequently driving growth and achievement.
- Whole Melt Bulk's
- furnish a solution for optimized production.
- Empowering advanced manufacturing processes.